In the dynamic realm of modern manufacturing, where every second counts and efficiency reigns supreme, the Industrial Internet of Things (IIoT) emerges as a transformative force. IoT in Manufacturing is not just about machines and data; it’s about revolutionizing the way factories operate, making them smarter, more efficient, and cost-effective.
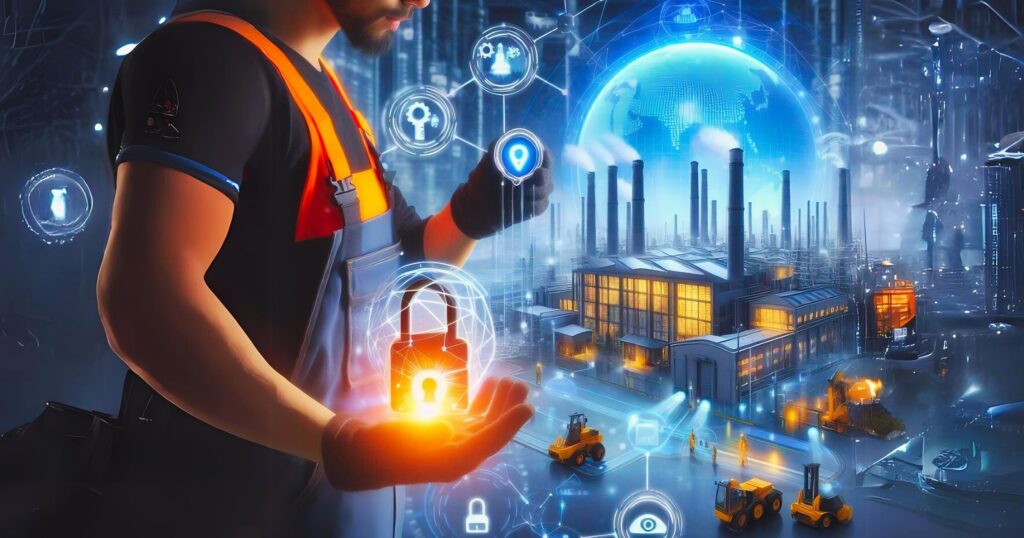
Imagine a factory floor where machines converse fluently, orchestrating their activities autonomously. This isn’t science fiction; it’s the reality of connected manufacturing through IoT sensors.
In this article, we delve into the profound impact of IIoT on the manufacturing industry. Buckle up as we explore how IoT supercharges efficiency, slashes costs, and propels factories into the era of Industry 4.0. From predictive maintenance to digital twins, we’ll unravel the intricacies of this technological revolution.
Let’s delve into how IIoT supercharges efficiency and slashes costs across the manufacturing sector.
The Impact of IoT in the Manufacturing Industry
- Efficiency and Productivity: Imagine a factory floor where machines communicate seamlessly, orchestrating their activities autonomously. This is the power of connected manufacturing through IoT sensors. These sensors enable real-time data exchange, allowing machines to optimize their performance. A McKinsey report predicts that IoT applications in manufacturing could generate a staggering $1.2 to $3.7 trillion annual impact by 2025. This translates to a massive boost for the manufacturing industry, potentially unlocking trillions of dollars in economic value. Efficiency gains are not just incremental; they’re transformative.
- Predictive Maintenance: Predictive maintenance, fueled by IoT technologies, is a game-changer. By analyzing data from sensors, manufacturers can predict equipment failures before they happen. Imagine slashing breakdowns by 70% and cutting maintenance costs by 25%! That’s the power of predictive maintenance, according to Deloitte. Imagine the savings and uninterrupted production cycles!
- Energy and Sustainability: IoT isn’t just about machinery; it’s about resource optimization. Even portable toilet companies are going green! Armal, a manufacturer in this industry, used real-time data to cut their energy use by almost 40%. Imagine what this technology can do for your factory. Sustainable practices are no longer a luxury; they’re a necessity for competitive manufacturing.
- Supply Chain Optimization: In today’s fast-paced world, supply chains need to be agile. IoT solutions enhance operational efficiency, improve production speeds, and automate repetitive tasks. 78% of supply chain leaders seek technology to achieve these goals. Nearly 8 out of 10 supply chain leaders are looking to unlock the efficiency and speed of tomorrow’s factories. That’s where IoT comes in. By automating repetitive tasks, optimizing operations, and accelerating production, IoT solutions are the key to gaining a competitive edge. The connected factory ensures smoother logistics and reduced lead times.
Industry 4.0 and Beyond
Industry 4.0 isn’t a distant dream; it’s here. The convergence of IoT, cloud computing, and machine learning has birthed smart manufacturing. Factories are no longer just assembly lines; they’re intelligent ecosystems. Let’s explore what drives this transformation:
- Smart Manufacturing: It’s not just about making things; it’s about making them smarter. Smart factories optimize processes, minimize waste, and adapt swiftly to changing demands.
- Data Analytics in Manufacturing: Data isn’t just raw numbers; it’s actionable insights. Analyzing production data helps factories make informed decisions, spot trends, and fine-tune operations.
- Cloud Computing in Manufacturing: The cloud isn’t just for storage; it’s a dynamic platform for real-time collaboration, scalability, and remote monitoring. It’s where data becomes accessible power.
- Machine Learning in Manufacturing: Machines learn from data, adapt, and improve. Whether it’s quality control or demand forecasting, machine learning optimizes processes.
- Digital Twin: Imagine a virtual replica of your factory. Digital twins simulate real-world scenarios, allowing manufacturers to test changes, predict outcomes, and optimize performance.
The era of smart manufacturing is upon us. IIoT isn’t just a buzzword; it’s a revolution. As factories embrace these technologies, they unlock efficiency, reduce costs, and pave the way for a sustainable future. So, gear up for Industry 4.0 – where machines don’t just produce; they innovate!
Innovative Use Cases for Modern Manufacturing
Imagine a factory that can predict problems before they happen, optimize production on the fly, and even catch human errors before they cause issues. That’s the power of modern manufacturing! Here’s how some innovative technologies are changing the game:
- Say Goodbye to Downtime:
- Smart machines: Sensors embedded in equipment track things like vibration, temperature, and energy use. This allows advanced software to predict breakdowns before they occur, preventing costly downtime.
- Real-time insights: Manufacturers can constantly monitor their factory floor, making quicker and more informed decisions to keep things running smoothly.
- Optimizing Production for Maximum Output:
- No bottlenecks here: With a constant stream of data, manufacturers can identify areas slowing down production. Adjustments can be made to maximize output and keep everything flowing efficiently.
- Machine performance at your fingertips: Track individual machine performance in real time to identify any underperformers or machines needing adjustments. This ensures optimal use of resources.
- Human Error? No More!
- Automating repetitive tasks: Manufacturing often involves repetitive tasks like moving materials or operating machines. These tasks are prone to errors. Luckily, the Internet of Things (IoT) can automate these tasks, eliminating human error entirely.
- Making Smarter Decisions with Real-Time Data:
- Instant insights: IoT and other data-generating technologies provide manufacturers with a constant stream of real-time data. This allows for immediate insights to make faster and more accurate decisions on the factory floor.
- Saving Money While Making Great Products:
- Reduced costs: IoT helps prevent equipment failures that can halt production and waste money. It also allows for just-in-time deliveries, reducing storage costs. Additionally, by analyzing quality control data, manufacturers can identify and fix problems early, reducing scrap and rework costs.
- Sensors: The Eyes and Ears of Your Factory:
- Monitoring everything: Sensors can track machine temperatures, vibration levels, pressure, and even product quality throughout the production line. This allows for early detection of issues and ensures consistent high-quality output.
- Supply Chain Smoother Than Ever:
- Real-time tracking: Imagine a network of sensors following your products everywhere – from warehouses to trucks. This allows for real-time location tracking, optimized delivery routes, and ensuring proper storage conditions for all your goods.
These are just a few examples of how modern manufacturing is using cutting-edge tech to become more efficient, cost-effective, and reliable. The future of manufacturing is bright, and it’s all thanks to innovation!
Industrial Future Using IoT Data Analytics
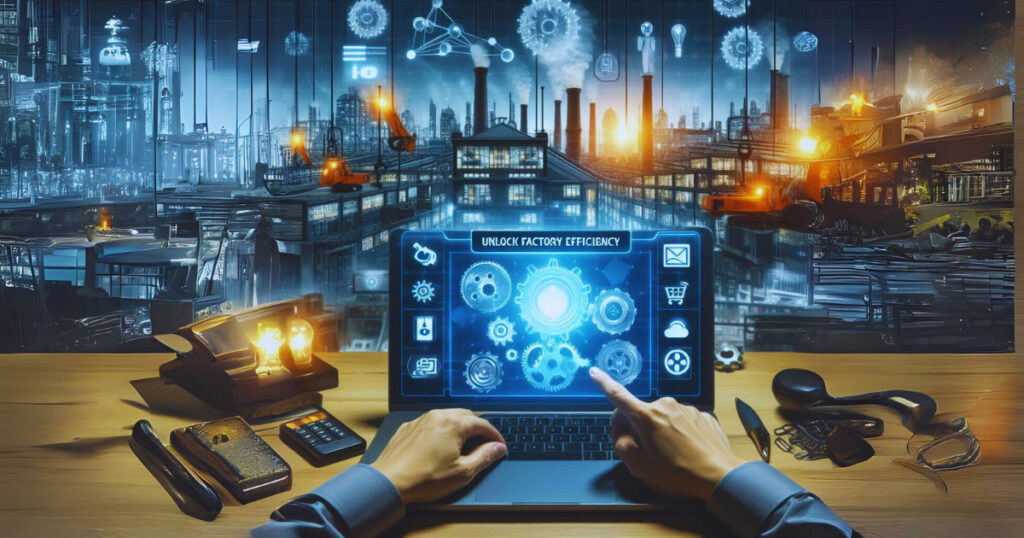
The future factory floor is a symphony of interconnected devices, each playing its part. Sensors embedded in machines become the factory’s nervous system, feeding real-time data into a central hub.
Here, advanced analytics algorithms become the brain, interpreting the whispers and turning them into actions. Predictive maintenance becomes the norm, with machines serviced before a breakdown disrupts the flow.
Inventory, once a guessing game, transforms into a precisely orchestrated dance, with materials arriving just in time to eliminate waste. The physical walls of the factory dissolve in this future, replaced by a digital tapestry woven from real-time data.
Imagine holographic projections of assembly lines overlaid on the physical world, highlighting bottlenecks and inefficiencies. Engineers, no longer confined to a single location, collaborate virtually from anywhere on the globe, manipulating these digital phantoms to optimize production.
Augmented reality headsets transform factory workers into walking instruction manuals, with critical information and repair procedures superimposed on their field of vision. The factory itself becomes a living organism, constantly learning and evolving, adapting to market demands with the agility of a digital chameleon.
Renowned companies using IoT in manufacturing
- Industrial Automation Giants: Siemens, Bosch, ABB, Rockwell Automation (These companies are at the forefront of providing industrial automation solutions that integrate seamlessly with IoT)
- Tech Titans: IBM, Microsoft, Amazon (These tech giants offer powerful cloud platforms for building and deploying industrial IoT applications)
- Manufacturing Powerhouses: General Electric (GE), Caterpillar, Boeing (These companies are leveraging IoT to optimize their manufacturing processes and develop innovative products)
- Aerospace Leaders: Airbus (Airbus is a prime example of a company using IoT to create its “Factory of the Future”)
This list is not exhaustive, but it highlights some of the major players who are shaping the future of manufacturing with IoT.
Read: What Innovation Changed the Textile Industry?
Challenges of Integrating IoT in Manufacturing
Every invention has some drawbacks; the goal is to overcome these drawbacks to achieve desired outcomes. Despite these challenges, the potential benefits of IoT in manufacturing are undeniable. By addressing these hurdles, manufacturers can cultivate a future of industrial excellence, ripe with efficiency, productivity, and innovation.
However, here are some issues that we should handle carefully to prevent any unintended consequences.
- Security Vulnerability: Imagine a vast network of interconnected devices – a treasure trove for cybercriminals. With increased connectivity comes a magnified risk of cyber-attacks. Manufacturers need robust security measures to protect sensitive data and prevent disruptions to critical operations.
- Data Deluge: IoT devices generate a massive amount of data. Imagine factories overflowing with information – sensor readings, performance metrics, and equipment logs. Manufacturers need data management strategies to store, analyze, and extract value from this data deluge.
- Interoperability Blues: Picture a factory floor where devices speak different languages. A lack of standardized protocols across manufacturers and devices can lead to integration headaches. Imagine sensors not communicating effectively or struggling to connect with existing systems. Finding solutions that ensure seamless communication between devices is crucial.
- Costly Cultivation: Implementing IoT can be an expensive proposition. Imagine the initial investment in sensors, data infrastructure, and security measures. The cost of integrating and maintaining this new ecosystem needs careful consideration.
- Workforce Weeds: New technologies require a skilled workforce. Imagine a gap between existing skills and the demands of IoT-driven manufacturing. Manufacturers need to invest in training programs to equip their workforce with the skills needed to manage and optimize IoT systems.
Conclusion
The integration of IoT technology into manufacturing processes heralds a profound transformation in the industry. Through real-time data monitoring, predictive analytics, and seamless connectivity, IoT empowers manufacturers to optimize operations, enhance efficiency, and drive innovation.
From predictive maintenance and supply chain optimization to smart factories and personalized production, the potential of IoT in manufacturing is vast and far-reaching. Embracing IoT not only unlocks new levels of productivity and competitiveness but also fosters a paradigm shift towards agile, sustainable, and customer-centric manufacturing ecosystems.
As we stand at the brink of this technological revolution, harnessing the power of IoT is not merely an option but an imperative for manufacturers aiming to thrive in the dynamic landscape of the future.
What is IoT in manufacturing?
Imagine your factory floor as a living organism. IoT equips this organism with a nervous system of sensors that collect data on its health and performance. This data is then analyzed by a central brain (the analytics platform) that generates insights on how the organism can function more efficiently. The result? A smarter factory that optimizes production, minimizes waste and keeps downtime to a minimum.
How does IoT help in manufacturing?
IoT acts as a digital nervous system for your factory. Sensors collect a wealth of data on everything from machine performance to environmental conditions. This data is then analyzed to identify areas for improvement. IoT can:
Increase efficiency: By optimizing production processes and identifying bottlenecks.
Improve production speeds: Through real-time monitoring and adjustments based on data.
Automate tasks: Repetitive tasks can be automated, freeing up workers for more complex activities.
Reduce waste: By optimizing material usage and identifying areas of excess.
Improve inventory management: Real-time data allows for better forecasting and minimizes the risk of stockouts or overstocking.
How is IoT used in manufacturing?
Here’s a breakdown of the typical IoT setup in manufacturing:
Sensors: These are installed on machines and throughout the factory floor. They collect data on things like temperature, vibration, and energy consumption.
Gateways: These devices aggregate the data from the sensors and transmit it securely to the cloud.
Analytics Platform: This platform analyzes the data from the sensors to identify trends, predict issues, and generate insights.
User Interface: This interface allows operators to visualize the data and take action based on the insights generated.
How to implement IoT in manufacturing?
There’s no single approach, as it depends on your specific needs. However, there’s a general roadmap:
Identify areas for improvement: Start by pinpointing areas where efficiency can be boosted or downtime reduced.
Choose the right sensors and software: Select sensors that gather relevant data and choose software that integrates with your existing systems.
Develop a plan for data security: Ensure your data is protected from cyber threats.
Integrate the system with existing infrastructure: Connect the IoT system to your existing manufacturing software and equipment.
Train your workforce: Employees need to understand how to use the new system and interpret the data it generates.
How can IoT minimize downtime in manufacturing?
Traditionally, maintenance happens on a schedule or after a breakdown occurs. IoT sensors embedded in machines collect real-time data on performance and wear. By analyzing this data, manufacturers can predict equipment failures before they happen. This allows for preventative maintenance, catching problems early and fixing them before they cause costly downtime.
Very nice write-up. I definitely love this site. Continue the good work!
My web site: vpn special code